

Client Testimonials
Trusted by Innovators Across Industries
Lets remove that leap of faith when it comes to choosing a manufacturing partner. We shall let our results and our clients do the talking.

01
Prime Project Management
Service: Bespoke Batch Production, CAD optimisation
Scope: 300 units across three part families
Lead Time: 14 Days
Challenge & Solution
Prime Project Management required rapid prototyping that could scale seamlessly into low-volume batch production. They supplied a rough CAD model. Using our CAD design service refined the model for 3d printing, saving them money and time.
Process Steps
-
CAD review: Freddy analysed models to ensure manufacturability
-
Rapid Prototyping runs: Initial FDM prototypes verify to fit before the full batch
-
Batch Production: Full Scale Delivery
Key Outcomes
-
12% Per unit cost savings versus the original CAD model
02
Polish Interior

Service: Full CAD design, rapid FDM prototyping
Scope: 3 bespoke ABS extrusion profiles
Lead Time: 48 hours
Challenge & Solution
Polish Interior needed three unique exterior trim profiles in ABS for an exterior building. Starting from hand-drawn sketches, our in-house 3d modelling team created watertight CAD files.
Process Steps
-
Sketch-to-CAD: Conversion of sketches into SolidWorks models.
-
FEA & DFM: Ensured extrusion sections would not collapse or warp.
-
Prototype runs: Three profiles printed overnight for onsite test.
-
Revision cycle: Two iterative refinements based on client feedback.
-
Final delivery: ABS, Vapour smoothed
Key Outcomes
-
3 Complete Iterations delivered within 48 hours

03
Knee System
Service: CAD modelling → Prototyping → Post-finish
Scope: Display model of knee-replacement component
Lead Time: 4 weeks
Challenge & Solution
Knee Systems required a to-scale model, an anatomically accurate display for surgeon engagement.
Key Outcomes
-
100% Surgeon Approval
04
Bournemouth University
Service:on-demand rapid prototyping
Scope: 6-month partnership; 20+ prints per week
Lead Time: 6-months
Challenge & Solution
Bournemouth University’s mechanical engineering students needed a manufacturer for the IMechE Challenge
Process Steps
-
Weekly Print Runs: Same day prints
-
IMechE Challenge Support: Rapid prototyping of final entries.
-
Feedback Loops: Iterative refinement based on test results.
Key Outcomes
-
The team placed in the top 10 of the IMechE challenge.
-
40 iterations in 2 weeks
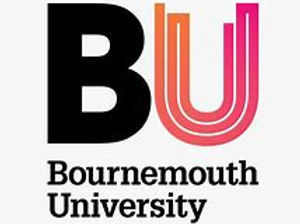

05
Digital Factory
Service:Rapid FDM printing, light finishing
Scope: 15 detailed cosplay parts
Lead Time: 2 months
Challenge & Solution
Digital Factory needed some STL files printed, ready for an exhibition show
Process Steps
-
Rhino Modelling: Organic geometry cleanup and shelling for hollow parts.
-
Slicing Profiles: Tuned for overhangs and surface quality.
-
Prototype Runs: PLA+ for general shapes, PET-G for wear-resistant clips.
Key Outcomes
-
30% Cost savings vs conventional prop fabrication
06
Stour Carp

Service: End-to-end CAD design, prototyping
Scope: Weatherproof lake feeder prototype
Lead Time: 10 months
Challenge & Solution
Stour Carp needed a solar-powered, weatherproof feeder that could withstand UV, moisture and variable temperatures. Along with members at Stour Carp, we created a sealed housing with integrated solar mounts and servo interfaces.
Process Steps
-
Concept CAD & Simulation: UV and thermal stress analysis in SolidWorks.
-
First-Pass Prototype: ASA-UV printed for initial field trial.
-
Iteration: Adjusted gasket interfaces and Carp feed trajectory
-
Final Prototype
Key Outcomes
-
100% Caro Fish Satisfaction
Ready to become our next success story?
Talk to and will give you our advise on the best way forward for your project